Understanding Welding WPS Requirements: Ideal Practices and Techniques for High Quality Welds
In the realm of welding, mastering Welding Treatment Spec (WPS) standards is a critical component that straight affects the quality and stability of welds. As we browse through the ins and outs of welding WPS criteria, discovering vital insights and methods for accomplishing top-tier welds will certainly be critical for welders seeking to stand out in their craft and create welds that stand the test of time.
Recognizing Welding WPS Specifications

Examiners rely on WPS documents to validate that welding procedures are being followed properly and that the resulting welds are of high top quality. Engineers make use of WPS criteria to develop welding treatments that ensure the durability and integrity of bonded structures.
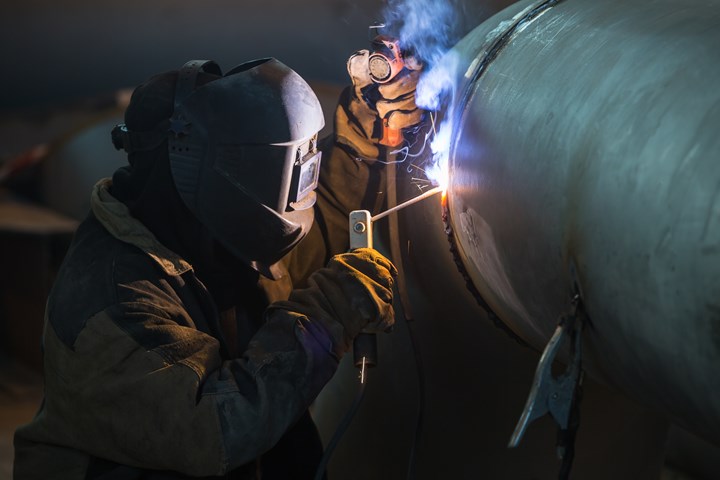

Vital Devices for Top Quality Welds
Mastering welding WPS criteria is essential for welders to properly utilize the important tools needed for creating high quality welds. The kind of welding maker required depends on the welding procedure being utilized, such as MIG, TIG, or stick welding. Cord brushes and cracking hammers are vital for cleaning up the weld joint before and after welding to eliminate any type of contaminations that can affect the top quality of the weld.
Key Techniques for Welding Success
To achieve welding success, one must master the essential methods crucial for producing high-quality welds. One crucial method is keeping the correct arc size. Keeping the electrode at the optimum distance from the work surface is vital for producing strong, uniform welds. In addition, controlling the traveling rate is paramount. Moving too swiftly can result in not enough infiltration, while relocating as well slowly can bring about excessive warm input and possible issues. Correct control of the electrode angle is an additional vital method. The angle at which the electrode is held can impact the grain shape and infiltration of the weld. Moreover, making sure consistent weapon angle and direction of travel is vital for uniformity in the weld grain. Finally, preserving a constant hand and a secure welding placement throughout the procedure is vital to accomplishing accuracy and consistency in the welds. By understanding these essential methods, welders can boost the quality of their work and attain welding success.
Ensuring Compliance With WPS Standards
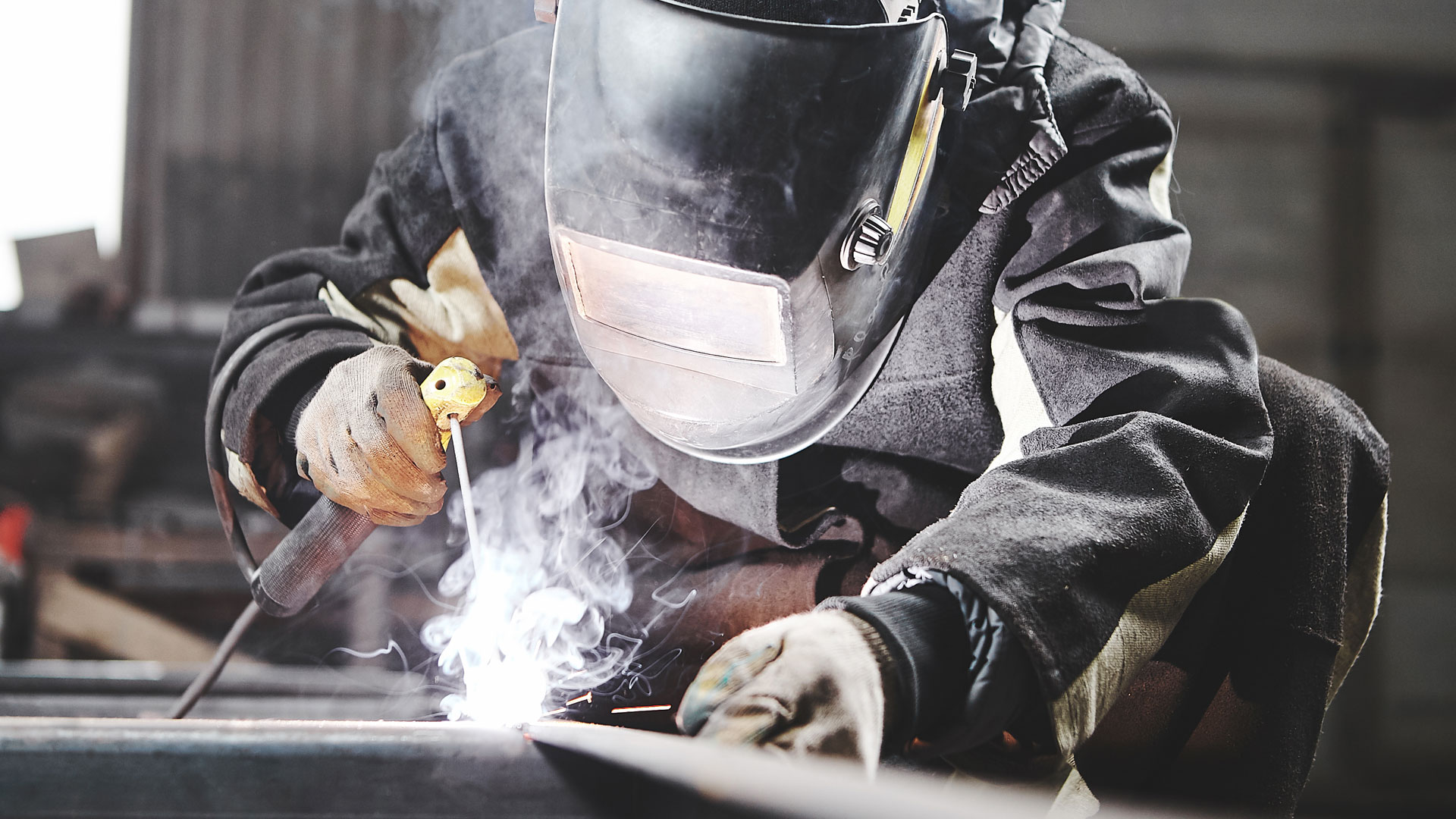
Additionally, keeping in-depth documents of welding parameters, tools calibration, and assessment outcomes is crucial for demonstrating compliance with WPS standards. By carefully sticking to WPS criteria, welders can ensure that their job fulfills the required top quality degrees and contributes to the overall success of the welding job.
Troubleshooting Common Welding Issues
When confronted with usual welding problems, determining the source is important for reliable troubleshooting. One prevalent issue is the visibility of porosity in welds, typically triggered by pollutants such as oil, rust, or moisture. To address this, making sure correct cleansing read here of the base steel prior to welding and making use of the correct shielding gas can considerably lower porosity. Another concern frequently experienced is lack of combination, where the weld fails to appropriately bond with the base product. This can stem from poor heat input or inappropriate welding method. Readjusting specifications such as voltage, cord feed rate, or travel speed can help enhance combination. In addition, distortion, breaking, and spatter prevail welding challenges that can be minimized via correct joint preparation, regular heat control, and choosing the suitable welding consumables. By completely understanding these common welding issues and their origin creates, welders can successfully troubleshoot issues and attain top quality welds.
Conclusion
In verdict, grasping welding WPS criteria needs a find out here comprehensive understanding of the guidelines, utilizing crucial tools, and applying key strategies for successful welds. Making certain compliance with WPS standards is vital for creating high quality welds and staying clear of usual welding issues. By following finest methods and strategies, welders can accomplish reputable and constant lead to their welding tasks.
In the realm of welding, mastering Welding Treatment Requirements (WPS) standards is an important part that directly influences the top quality and integrity of welds.When delving right into the world of welding techniques, a critical facet to comprehend is the importance and intricacies of Welding Procedure Specification (WPS) requirements. WPS criteria supply a comprehensive guideline for welding operations, ensuring consistency, high quality, and security in the welding procedure. The type of welding machine required depends on the welding procedure being utilized, such as MIG, TIG, or stick welding.Achieving welding success through the proficiency of essential techniques demands an extensive understanding and adherence to Welding Procedure Requirements (WPS) criteria.